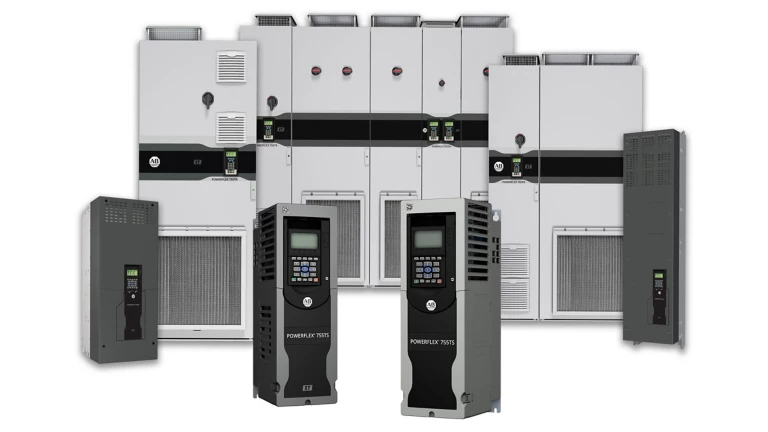
2025-04-22
Ensuring optimal performance in industrial environments starts with keeping your Allen-Bradley drives running smoothly. This comprehensive guide outlines how to troubleshoot common drive issues, interpret fault codes, and fine-tune system performance. Whether you're working with encoderless setups, dealing with overloads, or facing direction and speed issues, this post offers expert insight into keeping your drives operational and reliable.
Understanding Fault and Warning Indicators
Allen-Bradley drives feature diagnostic lights on the Velocity Processor (VP) and Current Processor (CP) to quickly communicate system health:
-
Solid Green: Normal operation
-
Flashing Green: Warning condition detected
-
Flashing Red: Soft fault condition
-
Solid Red: Hard fault that requires a reset or power cycle
Use the Human Interface Module (HIM) to:
-
Navigate to Control Status → Fault Queue
-
View up to 32 logged faults, each with a trip indicator and timestamp
-
Clear the fault or warning queue from the same menu
Common Fault Codes and Fixes
-
01027 – Autotune Diagnostic (Soft Fault)
Cause: Autotune test failure
Action: Rerun autotune and check for configuration errors -
01051 / 01083 – Motor Overload Pending (Soft Fault / Warning)
Cause: Load nearing overload threshold
Action: Adjust accel/decel settings or reduce motor load -
01052 – Motor Overload Trip (Soft Fault)
Cause: Overload limit exceeded
Action: Follow actions from 01051 -
01053 – Motor Stall (Soft Fault)
Cause: Stall duration exceeded
Action: Check torque limit status and adjust motor parameters
Start-Up Troubleshooting
-
Startup Procedure Not Accessible
Cause: Incompatible HIM version
Fix: Confirm HIM series/version from device label -
Feedback Loss Fault
Cause: Disconnected encoder
Fix: Reconnect and configure encoder -
No Motor Rotation During Phase Test
Cause: Load or autotune issues
Fix: Rerun autotune without load, test inertia -
Repeated Encoder Lead Switch Requests
Cause: Missing feedback
Fix: Check connections and validate motor speed (target 90 RPM for 60 Hz 4-pole motor)
Additional Troubleshooting Areas
Drive Start/Stop and Speed Issues:
-
Verify proper 2-/3-wire configuration and dwell time settings
-
Check speed references and stop type bits
-
Reset defaults and rerun startup if needed
Direction & Torque Problems:
-
Review settings for Ramp/ClrFlt Owner, Clr Flt/Res Mask, and SP Enable Mask
-
Ensure Logic Options don’t restrict direction changes
-
Confirm encoder settings and retune if overcurrent faults appear
External Inputs & Overload:
-
Validate SP An In1 and L Option Mode configurations
-
Adjust scaling in parameters 120–122
-
Reduce motor overload % or revise speed limits
Encoderless Mode Troubleshooting
For drives operating without encoders, consider the following adjustments:
-
Motor Not Accelerating
-
Increase Spd Desired BW
-
Raise Kp Freq Reg and current limits
-
-
Oscillating Motor After Target Speed
-
Decrease Spd Desired BW
-
Adjust Error Filter BW
-
-
Overspeed Trip on Startup/Reversal
-
Increase accel/decel time
-
Lower Spd Desired BW
-
Boost Kp Freq Reg
-
Conclusion
Systematic troubleshooting of Allen-Bradley drives helps maintain uptime and avoid costly failures. From fault diagnostics and encoder issues to advanced parameter tuning, addressing each area with care leads to optimized drive performance and extended equipment life.
Need help troubleshooting or replacing a drive? Contact PLG Automation today:
Email: sales@plgautomation.com
Phone: 800-906-9271